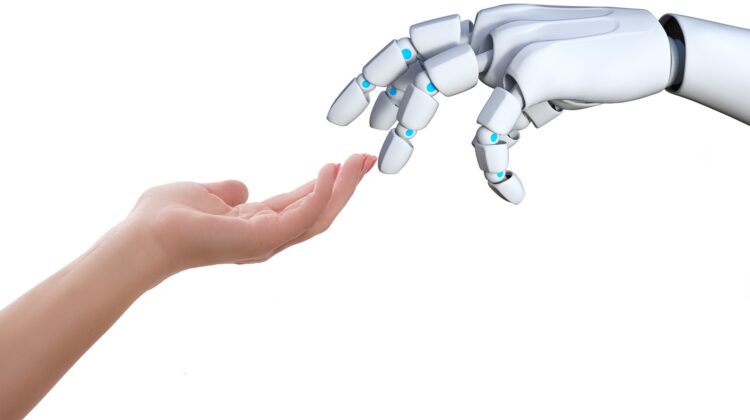
One of our editors, Swedish Concept Developer Healthcare, Maria Quinn – had the opportunity to be present during a robot assisting the surgeon in the Operating Room. Here are her thoughts and reflections on the sound environment in such a specialized area.
Robotic surgery
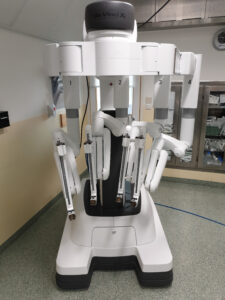
Robotic surgery, or robot-assisted surgery, allows doctors to perform many types of complex procedures with more precision, flexibility, and control than is possible with conventional techniques. Robotic surgery is usually associated with minimally invasive surgery. Procedures are performed through tiny incisions such as prostatectomies and increasingly for cardiac valve repair and gynecologic surgical procedures.
New technology brings forth new opportunities and challenges when incorporated into ongoing medical healthcare. What kind of effect can we for instance see in the design and planning of the actual operating room when this quite large device takes up space both during and after surgery? Will it affect the size of the optimally built room? Will it affect the sound environment in the room?
Sahlgrenska University Hospital
I had the opportunity to be present during a robotic surgery conducted at Sahlgrenska University Hospital in Sweden a couple of weeks back and I must admit it was impressive! The surgeon controlled the “arms” of the robot from a Virtual Reality console in a hut in the corner of the room whilst speaking into a microphone. The loudspeaker was placed on the upper part of the robot with the direction toward the rest of the team.
The sound environment
But concern had been expressed that the sound environment in this particular room was unsatisfactory so I conducted a sound pressure level (SPL) reading during the procedure (which was a removal of the prostate gland and the patient was fully sedated and wore hearing protection).
Some room details: it was a square room with 4 windows on the façade wall, 1 door towards the corridor, and 2 side walls. The ceiling consisted of plaster occupied by luminaires, pendulum mounts, and ventilation (picture 1). The only sound-absorbing material was two submerged beams with 20 mm absorbents along the side walls (picture 2). On one side, the immersion also included ventilation (4 rasters).
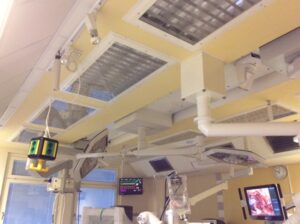
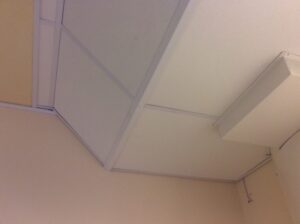
There was a total number of five staff; 1 surgeon, 2 surgical nurses, 1 anesthetic nurse, and 1 assistant auxiliary nurse.
Results
So what did it sound like? Well SPL varied between 56-64dB(A) but seemed to continue to stay in the upper level around the area of the surgical nurse closest to the patient. The reverberation time (T20) measured 0.43 seconds. Neither SPL nor RT seems to break the national building regulations for an operating room*.
However, the staff experience two real problems in the work environment. Firstly, pronounced fatigue after working in this particular OR. And secondly, difficulty hearing what was said during surgery. The nurse in the area of consistently higher SPL had trouble hearing what was said and she was the one co-working with the surgeon in the wound. The staff also stated that many high-frequency sounds from the med-tech equipment disturbed their concentration, This was particularly noticeable for anesthetic staff.
Frequencies and Signal-to-Noise Ratio
Looking at how the energy is distributed over the frequencies we find a high load around the lower frequencies. Which is well known to be tiring for personnel exposed to them for a longer period. The presence of low-frequency sounds also makes it difficult to hear the information-bearing consonants that have their largest range of energy around 500 Hertz. To be able to distinguish consonants from background noise, a Signal to Noise ratio (SNR) of 10-15 dB is required, i.e. it is difficult to hear consonants in the current environment. This correlates well with the staff’s expressed concerns about clearly hearing what the surgeon said!
What to do?
Even though building regulations weren’t exceeded when looking at the pure mathematics of it, staff still had a hard time working so what can be done? My thoughts on actions would include reviewing the possibilities of installing a full-length, sound-absorbing ceiling. But also installing wall absorbers that will affect the lingering horizontal reflections of sounds that disturb speech intelligibility. Second, the ventilation needs to be looked at and possibly adjusted.
The list can of course continue with ideas of adjustment of the med-tech equipment as well as human speech behavior but let´s stay within the building adjustments for now! I am excited to come back and do a follow-up, hopefully, we will see some good results and meet the really happy and content staff!
The future
I must say it´s a pretty amazing experience to stand beside a robot working on a human body. I think we will meet many new scenarios in the coming years that will push us to come up with innovative ideas and solutions to meet a changing world. I am happy to have met this particular robot (da Vinci**) and I know there are close to another 300 of them in Sweden. An exciting future lies ahead and don´t worry – every move was controlled by the well-prepared surgeon guiding the surgical robot and specifying what actions it was taking.
__________________________________________
*According to the Swedish Work Environment Authority AFS 2005: 16, there are recommendations regarding noise in complex tasks (more sensitive to disturbing sounds) and psychological effects (fatigue, irritation), and physiological (sympathetic addiction). It is also mentioned here that noise can mask speech. If there are staff with impaired hearing, these can especially experience negative effects and be particularly sensitive. Noise should be eliminated at the source and lowered to the lowest possible level. Airborne noise can be reduced by, for example, sound absorbers in the ceiling, on the wall, or as screens.
**the da Vinci Surgical System is a robotic surgical system made by the American company Intuitive Surgical. Approved by the Food and Drug Administration (FDA) in 2000, it is designed to facilitate complex surgery using a minimally invasive approach and is controlled by a surgeon from a console. According to the manufacturer, the da Vinci System is called “da Vinci” in part because Leonardo da Vinci‘s “study of human anatomy eventually led to the design of the first known robot in history.”